What is a masking agent? Principle, Role and Usage
Masking agents are substances that are resistant to physical and chemical elements such as heat, acids, alkalis, and solvents.
The purpose is to provide temporary surface protection by applying it to the part. The masking agent is applied to the area to be protected, and a surface treatment such as painting, plating, or melting is applied. When the masking agent is subsequently removed, a surface unaffected by the surface treatment appears. In this way, masking agents are used when you want to apply surface treatment only to the desired area.
When the masking agent is subsequently removed, a surface unaffected by the surface treatment appears. In this way, masking agents are used when you want to apply surface treatment only to the desired area.
Principles, roles and effects of masking agents
The most famous type of masking is masking tape.
Masking tape can be simply applied to prevent paint from sticking to the surface and create a clean finish.
On the other hand, our masking agent is a liquid masking agent made of special rubber dissolved in a solvent.
Since it is a liquid, it can be applied freely to components.
It is more resistant to physical and chemical elements than masking tape, and is less susceptible to high temperature environments and various chemical solutions.
After drying, the masking agent has sufficient strength and can be easily removed after surface treatment.
For more information on our masking agents, click here.Applications of masking agents
It can be used for various surface treatments. And we have Achievements in the following applications.
Electroless nickel plating
・Electroplating
・Hot dip zinc plating
・Hard chrome plating
・Anodizing
・Chemical polishing
・Electropolishing
・
Etching
・Chemical treatment
・Protection of plating jigs
MASKINGHow to use masking agents
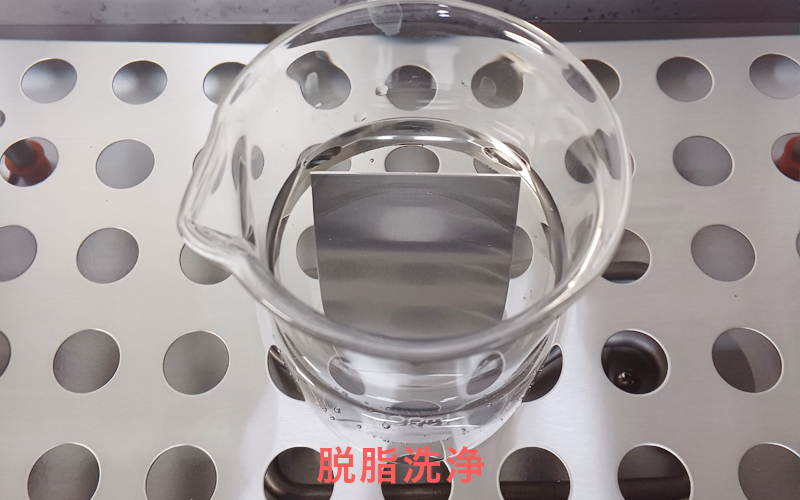
Improved protection functions
Degreasing and cleaning the parts before applying the masking agent will improve the adhesion and protection of the masking agent.
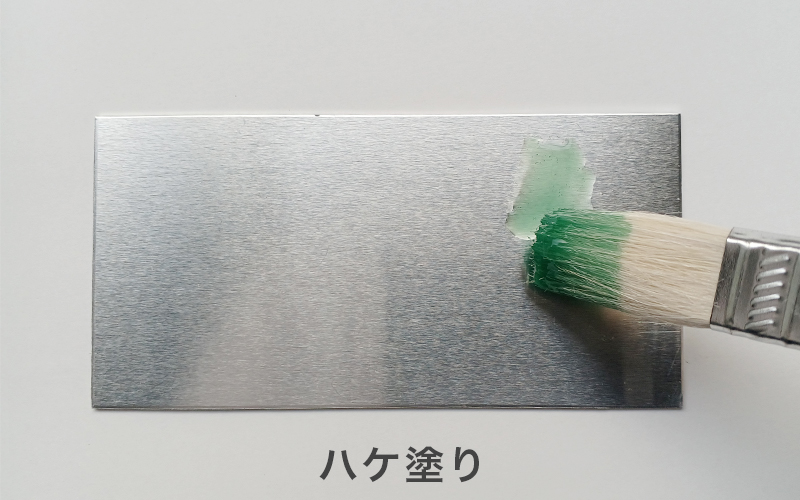
Apply masking agent
Apply the masking agent to the area to be protected on the part. The application method is generally by brush or dipping. After application, allow the masking agent to dry. Drying time varies depending on weather conditions and film thickness, but should be approximately 2 hours. Heating will shorten the drying time, but will increase the risk of ignition.
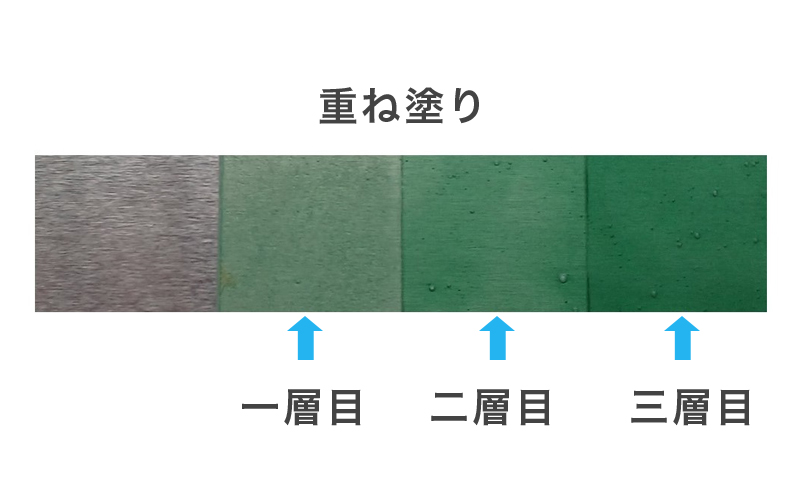
Overcoating
Two to three coats are recommended depending on the type of surface preparation. The protective effect is improved by applying two or three coats. When applying two or three coats, apply them after the coated surface has dried. The masking agent will be easier to remove after the work is completed.
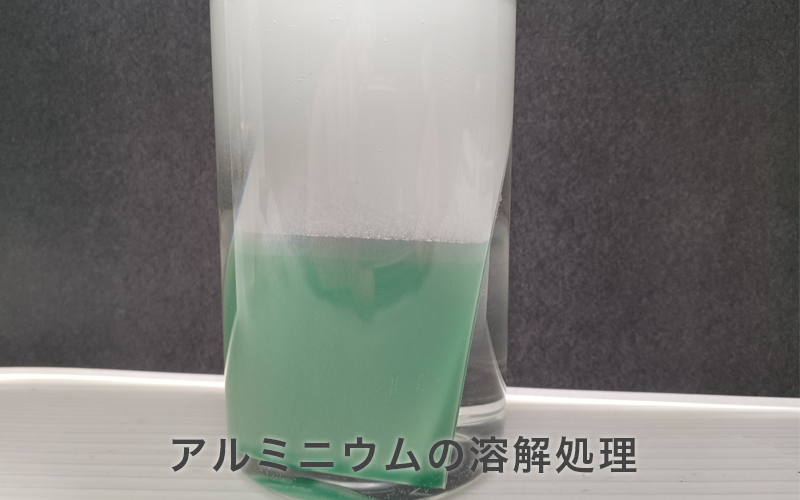
Surface Treatment
Provide the necessary surface treatment.
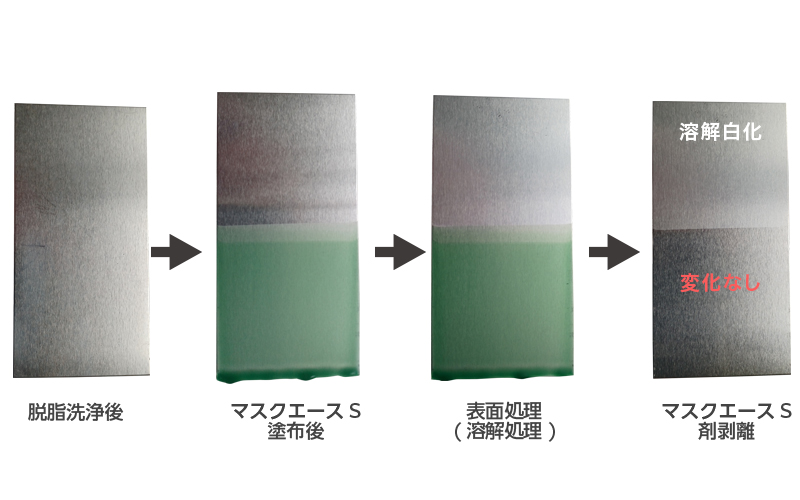
End of work
end of work All work is completed when the masking agent is removed. In the case of hot dip galvanizing, the masking agent may burn and carbonize, making it difficult to remove. In this case, please consider removal methods such as hard scrubbing or washing.
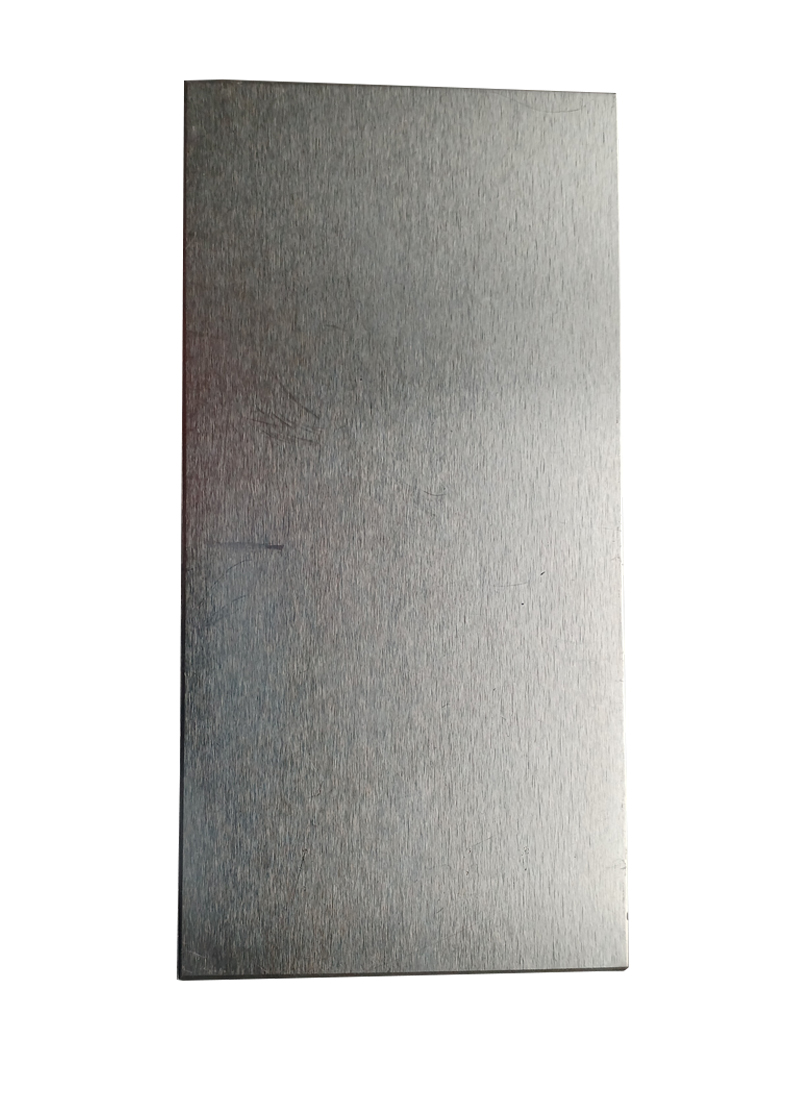
After degreasing and cleaning
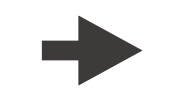
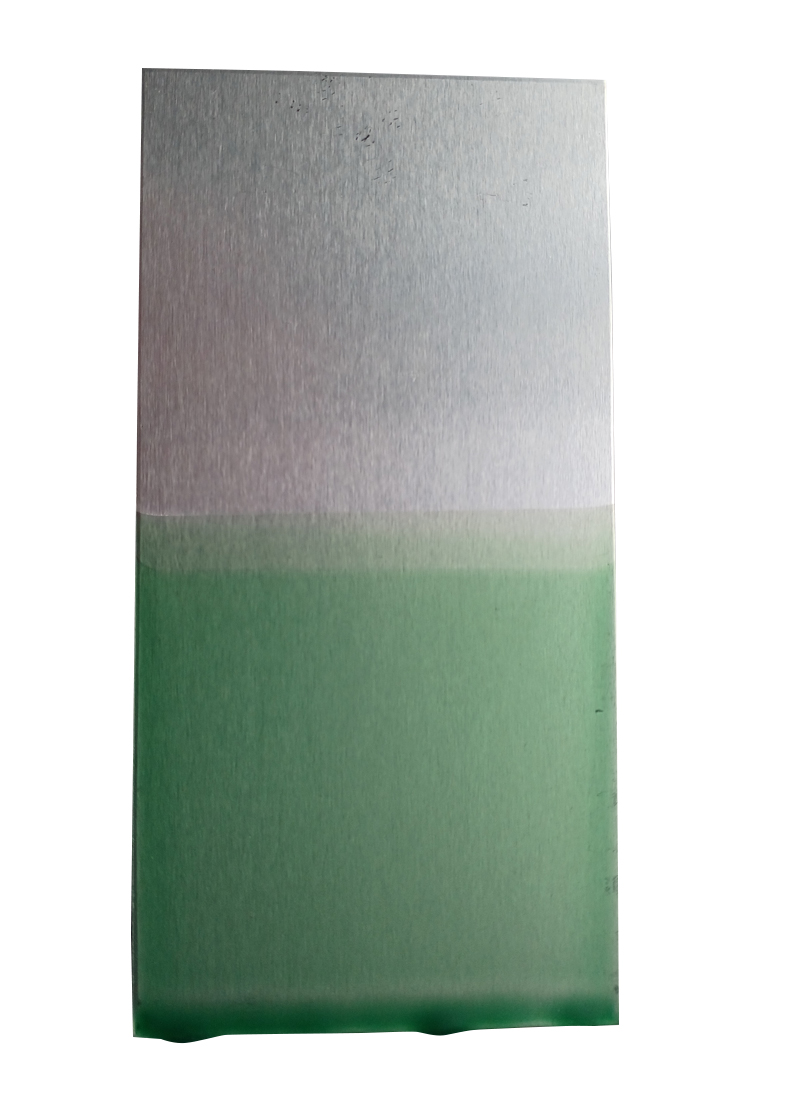
After application of Mask Ace S
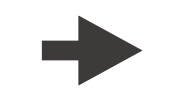
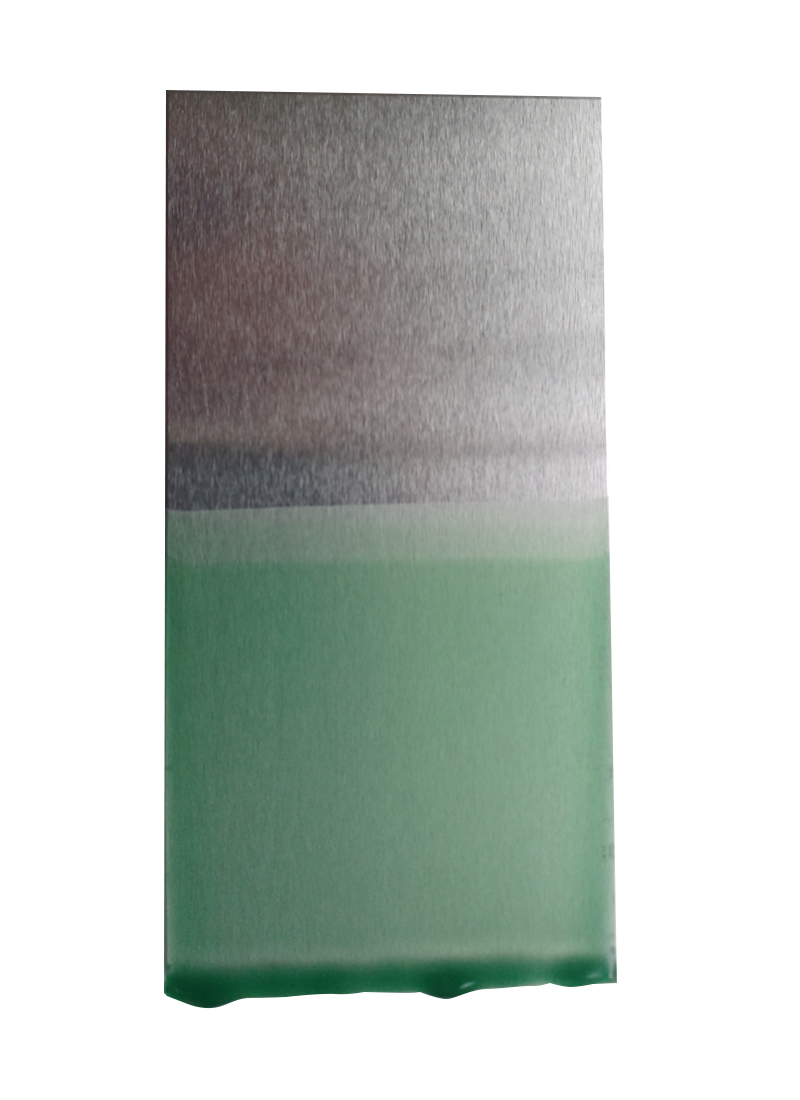
Surface treatment
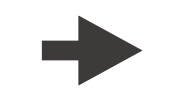
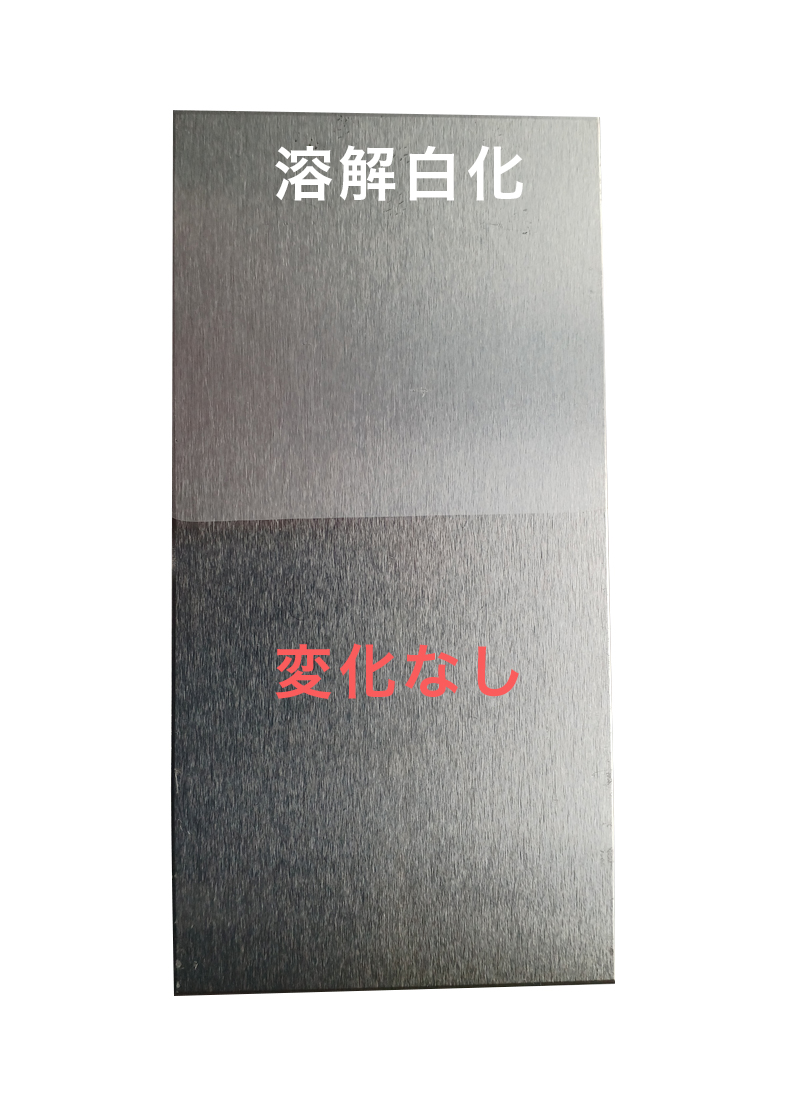
Removed off Mask Ace S.
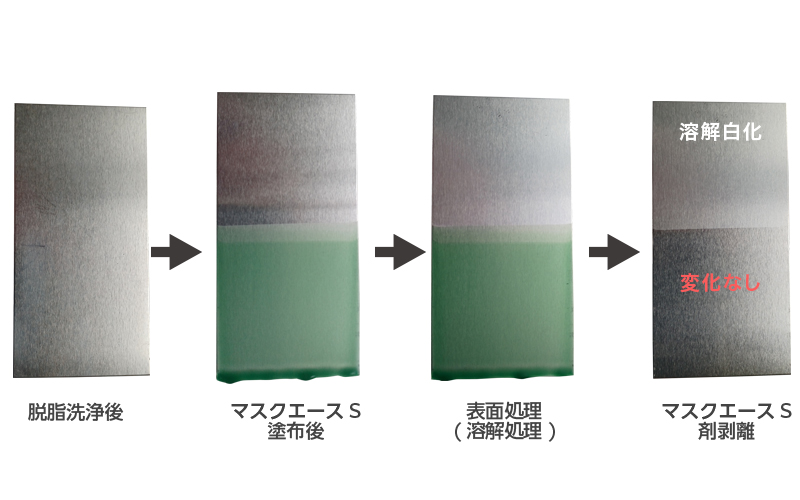

Cautions for use
This product is highly flammable and will catch fire even at low temperatures. Please apply and dry the product in a place where there is no fire or source of heat.
This product contains organic solvents, so protective equipment such as organic solvent masks, goggles, and gloves should be worn when handling this product. Make sure the work area is well ventilated.
Plastic will melt or deform if applied to plastic products such as plastic models. It may not be usable. For use on plastic products, test before use.
-
2-8-11 Higashi-Nihonbashi, Chuo-ku, Tokyo 103-0004 Japan
813-5687-1931 weekday9:00-17:00
813-5687-1933 24 hours reception
Contact Us
Product List
813-5687-1931